Last updated on
Electrical discharge machining (EDM) and conventional machining are two distinct manufacturing processes that are used to create parts and components from raw materials.
Both have their own unique set of advantages and disadvantages, and the best choice for your project will depend on a variety of factors.
If you’re wondering which of the two processes you should use, the following pointers can help you make an informed decision.
Table of Contents
Electrical Discharge Machining (EDM) In a Nutshell
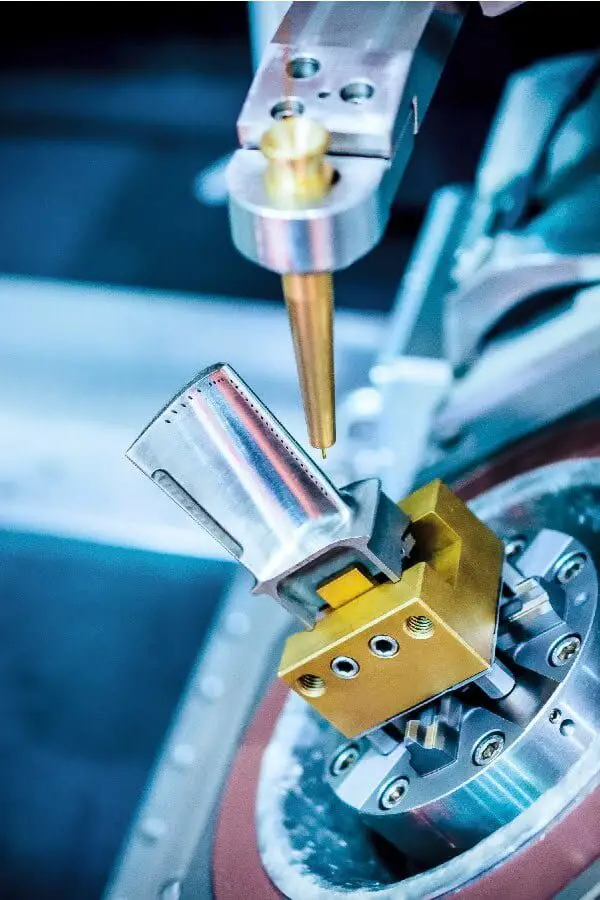
EDM is a non-traditional machining process that uses electrical discharges (sparks) to remove material from a workpiece. It is often used to machine parts from hard, electrically conductive materials such as steel, aluminum, and copper.
Also, EDM systems such as EDM sinkers and wire EDM are particularly effective at machining complex shapes and fine details. Moreover, EDM is capable of producing very high surface finishes.
Conventional Machining In a Nutshell
Conventional machining, on the other hand, uses tools such as lathes, milling machines, and drill presses to remove material from a workpiece. It is well-suited for a wide range of materials, including both ferrous and non-ferrous metals.
It can also be used to create a wide variety of parts and components. Conventional machining is generally faster and more cost-effective than EDM, but it may not be able to achieve the same level of precision or surface finish.
Deciding Which Method Is Best For Your Project
When choosing between EDM and conventional machining for your project, there are a few important factors to consider. From the project’s size to the complexity and the materials you intend to use, these include:
Material
The type of material you are working with will influence the choice of the machining process. EDM is well-suited for hard, electrically conductive materials, while conventional machining can be used on a wider range of materials.
Project Size and Complexity
EDM is particularly effective at machining small, complex parts. Conventional machining, on the other hand, is better suited for larger parts and simpler shapes. This makes the latter a bit more suitable for DIY projects that require machining or surface modification.
Tolerances
In machining, tolerances refer to the accuracy and precision of the machined parts. EDM can produce parts with very tight tolerances, as small as +/- 0.0001 inches in some cases. This makes it an excellent choice for producing parts with precise dimensions and features. However, EDM is often slower and more cost-intensive compared to conventional machining.
Surface Finish Requirements
A great perk of using EDM is that it often produces very high surface finishes. However, conventional machining may also achieve similar results with the right tooling and techniques.
Project Costs
Conventional machining is generally faster and more cost-effective than EDM. If time is of the essence, this means that conventional machining might be the better choice. However, this will in part depend on the specific requirements of your project.
Lead Time
The lead time for a project is the amount of time it will take to complete the machining process. EDM may have a longer lead time than conventional machining, depending on the complexity of the part and the availability of machining equipment.
Available Machining Equipment
The availability of EDM and conventional machining equipment may also influence your choice of the process to use. If you do not have access to EDM equipment, or your budget doesn’t permit it, you may need to use conventional machining instead.
Alternatively, you can consider searching online for sites that keep an inventory of used EDM’s as these are often cheaper. All the same, you’ll want to use a trusted vendor who stocks a variety of equipment types and assures superior quality.
Ultimately, the choice between EDM and conventional machining will depend on the specific requirements of your project. It may be necessary to use both processes in combination to achieve the desired result, or to use one process for certain features and another for others. If you can, it pays to consult with a manufacturing expert to determine the best approach for your project.